MANUAL HANDLING?
Manual handling is any activity that involves lifting, lowering, pushing, pulling, carrying, moving, holding or restraining. It may also include stretching and bending, sustained and awkward postures, and repetitive movements. Manual handling can result in musculoskeletal injuries to workers.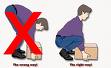
WHAT IS RISK MANAGEMENT?
Risk management is a step by step process to help employers identify, assess and then eliminate or control risks so as to avoid injury in the workplace. It is a practical way of finding and fixing workplace health and safety problems in consultation with workers.
WHAT DOES THE LEGISLATION SAY?
The Occupational Health and Safety Act 2000 (OHS Act) and the Occupational Health and Safety Regulation 2001 (OHS Regulation) set out the principles and requirements that apply to manual handling in the workplace.
Section 13 of the OHS Act requires employers to consult with their workers to enable them to contribute to decisions that affect their health, safety and welfare at work.
The OHS Regulation sets out the obligations of employers with respect to risk management. Risk management is the process of hazard identification, risk assessment and elimination or control of risks in the workplace.
Chapter 2 of the OHS Regulation outlines general risk management requirements and Chapter 4 relates specifically to manual handling. Clauses 79-81 of the OHS Regulation outline specific obligations regarding the management of manual handling risks in the workplace.
Clause 80 – Employer to control risks says:
• All objects, work practices and the working environment must be designed to eliminate manual handling risks • If elimination is not practical the risk must be controlled and, if necessary: − The design of objects or the work environment modified − Mechanical aids provided − Workers trained in safe techniques and correct use of mechanical assistance.
Clause 81 – Assessment of risks, says: • Employers are to carry out risk assessments and take into account the following risk factors: − Actions and movements − Workplace layout − Posture and position − Duration and frequency − Location and distance − Weights and forces − Characteristics of loads and equipment
− Work organisation − Work environment − Skills and experience − Age − Clothing − Special needs − Any other relevant factors.
The current National Code of Practice for Manual Handling is an approved code of practice under the OHS Act. It is practical guidance material and provides assistance for managing manual handling hazards. It outlines how employers, in consultation with those performing the tasks, should manage manual handling risks by:
• identifying possible problems • assessing the risks • eliminating the problem or providing mechanical assistance or lifting aids • Training workers in safer work practices • monitoring and reviewing the improvements.
Note: The National Standard and Code of Practice for Manual Handling and the National Code of Practice for the Prevention of Occupational Overuse Syndrome will be replaced by the National Standard for Manual Handling and the Code of Practice for the Prevention of Musculoskeletal Disorders from Manual Handling at Work in the near future.
FURTHER INFORMATION
• WorkCover Assistance Service 13 10 50 • www.workcover.nsw.gov.au • www.legislation.nsw.gov.au • www.ascc.gov.au (Office of the Australian Safety and Compensation Council) • www.standards.org.au (Standards Australia) • Employer organisations • Unions |